Ball Valves: A Versatile Solution for Fluid Control
Ball Valves: A Versatile Solution for Fluid Control
Blog Article
Ball valves are essential components in a wide range of industrial applications, known for their reliability and ease of operation. Designed to control the flow of fluids or gases, ball valves use a spherical disc, the “ball,” which has a hole through its center. When the valve is turned, this hole either aligns with or blocks the flow path, making the valve fully open or fully closed. This simple mechanism contributes to the ball valve’s high durability and widespread usage in industries such as oil and gas, water treatment, chemical processing, and manufacturing.
This article examines the functionality, types, advantages, and typical applications of ball valves, explaining why they are considered one of the most efficient fluid control devices in modern industry.
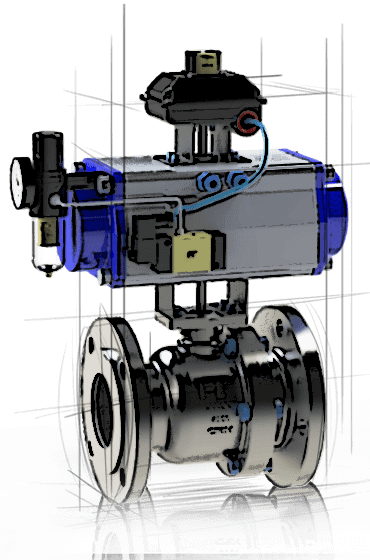
What Is a Ball Valve?
A ball valve operates by rotating a ball within a valve body, controlling the flow of fluids through a pipe. The ball has a hole, or port, which allows fluid to pass through when it is aligned with the inlet and outlet ports. When the ball is rotated by a quarter turn (90 degrees), the hole is perpendicular to the flow path, effectively stopping the flow. This straightforward on/off control is one of the ball valve’s defining characteristics, offering simplicity in design and operation.
Key Features:
- Quarter-Turn Operation: The valve requires only a 90-degree turn to fully open or close, making it quick and easy to operate.
- Tight Sealing: Ball valves provide a secure seal, even in high-pressure and high-temperature applications, reducing the risk of leaks.
- Versatile Applications: These valves are suitable for handling gases, liquids, and even certain slurries, thanks to their robust construction and efficient sealing.
Types of Ball Valves
Ball valves come in a variety of types, each designed to meet specific operational needs. Some common types include:
- Floating Ball Valve: In this design, the ball is suspended within the valve body and can float slightly. When the valve is pressurized, the ball is pushed against the downstream seat, creating a tight seal. Floating ball valves are typically used in lower-pressure applications, as they rely on pressure to maintain the seal.
- Trunnion Ball Valve: Trunnion ball valves are equipped with additional mechanical anchoring, known as trunnions, which support the ball in high-pressure conditions. This design helps prevent the ball from moving excessively under pressure, ensuring consistent sealing even in demanding environments. Trunnion ball valves are often found in oil and gas applications where higher pressure ratings are required.
- One-Piece Ball Valve: A one-piece ball valve is molded from a single piece of material, which makes it cost-effective and durable. However, it cannot be disassembled for repair, so it is usually replaced rather than serviced when needed.
- Two-Piece Ball Valve: This design consists of two separate pieces that are bolted together, allowing for disassembly, inspection, and cleaning. It provides more flexibility in maintenance compared to the one-piece design and is commonly used in applications where repairs may be necessary.
- Three-Piece Ball Valve: Three-piece ball valves are highly versatile and can be easily disassembled for maintenance or repairs without removing the entire valve from the pipeline. This design is beneficial in industries where frequent cleaning or servicing is required.
Materials and Coatings for Ball Valves
Ball valves are manufactured from various materials, depending on the requirements of the application. Common materials include:
- Stainless Steel: Known for its corrosion resistance and durability, stainless steel is suitable for most industrial applications, especially in harsh environments.
- Carbon Steel: Used in situations where cost-efficiency is important, carbon steel provides the necessary strength but may require additional corrosion protection.
- PVC and Other Plastics: Plastic ball valves are lightweight and corrosion-resistant, ideal for less demanding applications like water treatment and certain chemical processes.
Coatings such as PTFE (Teflon) are often applied to the ball to reduce friction and improve sealing. This coating helps extend the life of the valve, as it reduces wear and tear during operation.
Advantages of Using Ball Valves
Ball valves are popular for several reasons, as they offer a range of benefits that contribute to their efficiency and reliability in industrial settings.
- Durability and Reliability: Ball valves are known for their ability to withstand high pressure, high temperature, and corrosive environments. The tight seal provided by the ball and seat mechanism reduces wear, ensuring long-lasting performance with minimal maintenance.
- Quick Operation: The quarter-turn mechanism allows for fast opening and closing, enabling operators to control flow almost instantly. This feature is particularly valuable in applications where emergency shut-off capabilities are required.
- Versatile Applications: Ball valves can handle a variety of media, including gases, liquids, and slurries. This versatility makes them an excellent choice for applications in oil and gas, water treatment, pharmaceuticals, and more.
- Minimal Maintenance Requirements: With fewer moving parts than other valve types, ball valves are easier to maintain. Their simple design reduces the likelihood of failure, and the valves can often be serviced without removing them from the pipeline.
Common Applications of Ball Valves
Ball valves are found in a variety of industries due to their versatility and reliable performance. Some typical applications include:
- Oil and Gas: In this industry, ball valves are used in upstream, midstream, and downstream processes. Their durability and resistance to high pressure make them ideal for controlling the flow of crude oil, natural gas, and other hydrocarbons.
- Water Treatment: Ball valves control water flow in filtration systems, desalination plants, and sewage treatment facilities. They help ensure efficient water distribution and are resistant to corrosion, which is essential in water processing environments.
- Chemical Processing: Handling chemicals often requires a valve that can withstand corrosive materials and high temperatures. Ball valves made from stainless steel or PVC, with specialized coatings, are well-suited for these applications.
- Food and Beverage: The food processing industry uses ball valves due to their ability to maintain sanitary conditions. Stainless steel ball valves with food-grade seals are often used to control the flow of liquid ingredients and cleaning solutions.
Key Considerations for Selecting a Ball Valve
When choosing a ball valve for a specific application, several factors should be considered:
- Pressure and Temperature Requirements: Selecting a valve rated for the maximum pressure and temperature of the system ensures reliable operation under all conditions.
- Material Compatibility: Ensuring that the valve material is compatible with the media (fluid or gas) being transported is critical for preventing corrosion and maintaining valve integrity.
- End Connections: Ball valves come with various end connection options, such as threaded, flanged, and welded. Choosing the right type of connection can simplify installation and maintenance.
- Maintenance Needs: For applications where frequent maintenance is expected, a three-piece ball valve might be the best choice due to its ease of disassembly.
Installation and Maintenance Tips for Ball Valves
Proper installation and regular maintenance are essential for maximizing the lifespan and performance of ball valves. Here are a few tips:
- Install in the Correct Orientation: Ball valves should be installed in the orientation specified by the manufacturer to ensure optimal performance and minimize wear.
- Regularly Inspect for Leaks: Checking the valve for signs of leakage or corrosion helps catch potential issues early and prolongs the valve’s life.
- Clean Valve Interiors: For industries like food and beverage, where cleanliness is critical, regularly cleaning the valve’s interior can prevent contamination and maintain hygiene standards.
Conclusion
Ball valves have become indispensable in numerous industries, offering a durable, reliable, and easy-to-operate solution for fluid control. Their variety of designs and material options make them adaptable to almost any application, from oil and gas to water treatment and chemical processing. Choosing the right type of ball valve, ensuring proper installation, and maintaining the valve regularly are key to achieving optimal performance and longevity.
For industrial-grade Ball Valves that meet rigorous standards of quality and performance, consider Freture Techno Pvt. Ltd., a leading industrial valve manufacturer based in Mumbai, India.